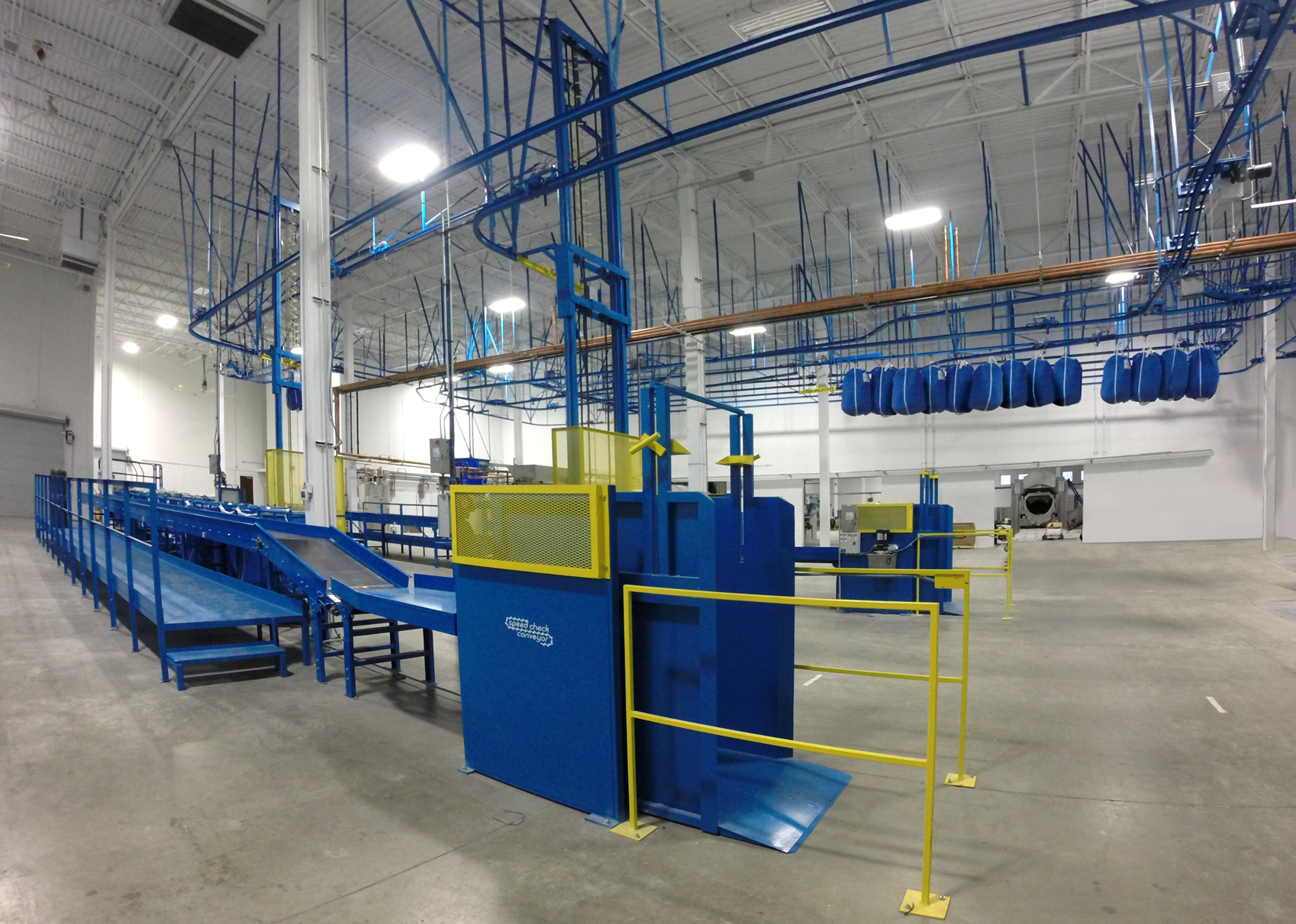
Frequently Asked Questions
Speed Check Conveyor welcomes your questions and looks forward to discussing your individual projects. Below are a few of the questions most frequently asked by customers.
All Speed Check equipment is designed to meet a heavy duty rugged construction for optimum performance within the caustic and challenging environment of a commercial/industrial laundry. Products are manufactured with quality materials to the highest standards providing maximum equipment life. Top priority to all designs are: operator ease-of-use, personnel safety features and easy/reduced maintenance.
The Speed Check Monorail is an all welded 3” steel I-Beam conveyor. Systems can be ceiling suspended or supported from the floor. All installations completed by experienced in-house staff or highly qualified factory-trained technicians.